The Future of Injection Molding: Trends and Innovations

The Future of Injection Molding: Trends and Innovations
Injection molding has been a cornerstone of the manufacturing industry for decades, providing efficient and cost-effective solutions for producing plastic parts. As technology evolves, so do the methods and materials used in injection molding. This article explores the latest trends, innovations, and best practices in the injection molding industry, ensuring you stay ahead of the curve.
Understanding Injection Molding
Injection molding is a manufacturing process that involves injecting molten material into a mold to create a specific shape. This method is widely used for producing plastic parts in various industries, including automotive, medical, and consumer goods. The process not only allows for high-volume production but also offers a level of precision that is crucial for many applications.
Key Benefits of Injection Molding
Injection molding offers several advantages that make it a preferred choice for manufacturers:
- High Efficiency: The process allows for rapid production of parts, significantly reducing cycle times.
- Cost-Effectiveness: Once the initial mold is created, producing additional parts becomes relatively inexpensive.
- Versatility: This process can accommodate a wide range of materials, including thermoplastics and thermosets.
- Precision: Injection molding produces parts with high dimensional accuracy, which is critical for many applications.
Current Trends in Injection Molding
The injection molding industry is experiencing several trends that are shaping its future. Understanding these trends can help manufacturers adapt and thrive in a competitive environment.
Sustainability Practices
Sustainability is becoming increasingly important in manufacturing. Companies are now focusing on eco-friendly materials and processes to reduce their environmental impact. This shift is not just a trend; it's a necessity for meeting regulatory standards and consumer expectations.
- Biodegradable Plastics: The use of biodegradable materials is on the rise, allowing for more sustainable product lifecycles. These materials break down more easily in the environment, reducing long-term waste.
- Recycling Initiatives: Many manufacturers are implementing recycling programs to reuse scrap materials and reduce waste. This not only conserves resources but can also lower production costs.
- Energy-Efficient Machines: New technologies are being developed to minimize energy consumption during the injection molding process, contributing to a smaller carbon footprint.
Automation and Industry 4.0
Automation is transforming the injection molding landscape. The integration of smart technologies enables manufacturers to optimize production processes and improve efficiency.
- Predictive Maintenance: IoT devices can monitor machine performance, predicting failures before they occur, thus minimizing downtime and repair costs.
- Data Analytics: Advanced data analytics help manufacturers make informed decisions based on real-time production data, leading to better resource allocation and reduced waste.
- Robotics: Automated systems and robots are increasingly used to handle repetitive tasks, improving efficiency and safety while allowing human workers to focus on more complex tasks.
Advanced Materials
The development of new materials is expanding the possibilities of injection molding. Manufacturers are exploring innovative options to meet diverse customer needs.
- High-Performance Polymers: These materials offer superior strength and heat resistance, making them ideal for demanding applications, such as automotive and aerospace components.
- Composite Materials: Combining different materials can enhance properties like durability and weight reduction, allowing for lighter and stronger parts.
- Smart Materials: These materials can change properties in response to external stimuli, opening new avenues for product design and functionality.
Best Practices for Cost-Effective Injection Molding
To maximize profitability, manufacturers must adopt best practices in their injection molding processes. Implementing these strategies can lead to significant improvements in efficiency and cost savings.
Design for Manufacturability (DFM)
Designing parts with manufacturability in mind can significantly reduce production costs. Simplifying designs can lead to lower tooling costs and faster production times. Additionally, selecting the right material can enhance performance while minimizing costs.
Optimize Production Processes
Streamlining production processes can lead to significant savings. Analyzing and optimizing cycle times can improve overall efficiency, while implementing rigorous quality control measures can reduce defects and waste.
Invest in Technology
Investing in the latest technologies can provide a competitive edge. Upgrading to energy-efficient and high-speed machines can enhance productivity, while utilizing software for simulation and design can reduce errors and improve outcomes.
Common Challenges in Injection Molding
Despite its advantages, injection molding comes with its own set of challenges that manufacturers must navigate. Understanding these challenges is crucial for developing effective strategies to overcome them.
Tooling Costs
The initial investment in molds can be substantial. However, this cost can be justified by the long-term savings in production. Manufacturers often need to balance the upfront costs with potential future savings.
Material Variability
Variations in material quality can affect the final product. Ensuring consistent material quality is crucial for maintaining standards and meeting customer expectations. Manufacturers must establish strong relationships with suppliers to ensure material consistency.
Production Downtime
Downtime due to maintenance or machine failures can impact profitability. Implementing predictive maintenance strategies can mitigate this risk, allowing manufacturers to address issues before they lead to significant downtime.
The Role of China in Injection Molding
China has emerged as a global leader in the injection molding industry, offering a combination of advanced technology and cost-effective production. Many companies outsource their injection molding needs to China due to lower labor costs and high-quality manufacturing capabilities.
Moreover, Chinese manufacturers are increasingly adopting advanced technologies, such as automation and smart manufacturing, to enhance their processes. This shift not only improves efficiency but also allows for greater flexibility in production.
For more insights on the role of China in injection molding, you can visit China injection molding.
Conclusion
The injection molding industry is evolving rapidly, driven by trends in sustainability, automation, and advanced materials. By adopting best practices and staying informed about industry developments, manufacturers can position themselves for success in this competitive landscape.
As you navigate the future of injection molding, consider the potential of innovative materials and technologies to enhance your production processes. For more information on plastic molds, check out plastic mold.
What's Your Reaction?
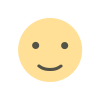
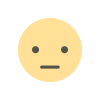
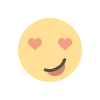
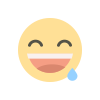
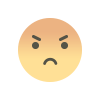
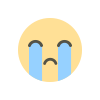
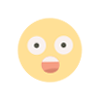