Quick and Easy 3D Printing Fixes to Improve Print Quality
A rough or inconsistent print surface can be caused by improper layer height settings, vibrations, or inconsistent filament flow.

One of the most common issues affecting print quality in 3D printing is improper bed leveling. If the print bed is not level, the first layer may not adhere properly, leading to warping or failed prints. A simple fix is to use the paper test method: place a piece of paper between the nozzle and the bed and adjust the bed height until the paper moves with slight resistance. Many modern printers also offer automatic bed leveling, which can significantly improve adhesion and consistency.
In addition to leveling, adjusting the Z-offset setting can help fine-tune the nozzle distance from the bed. If the nozzle is too close, prints may appear squished, and if it's too far, the filament may not adhere properly. Checking these settings before each print ensures better first-layer adhesion and ultimately improves the overall print quality.
Fixing Under-Extrusion and Over-Extrusion Issues
Under-extrusion occurs when the printer does not output enough filament, resulting in weak, incomplete prints with gaps between layers. A quick 3D Printing Fixes is to check the extruder tension, as a loose extruder gear can cause inconsistent filament flow. Additionally, increasing the printing temperature slightly can help ensure smooth filament flow. Cleaning the nozzle with a needle or using a cold pull method can also remove any blockages that may cause under-extrusion.
Over-extrusion, on the other hand, results in excess filament being deposited, leading to blobs and stringing. To fix this, calibrate the extruder steps-per-millimeter (E-steps) to ensure the printer is extruding the correct amount of filament. Reducing the flow rate in the slicer settings by 5-10% can also help prevent over-extrusion and improve the precision of prints.
Eliminating Stringing and Oozing
Stringing occurs when small strands of filament are left between parts of the print, usually due to excessive oozing. The easiest fix is to enable retraction in the slicer settings, which pulls the filament back slightly when the nozzle moves between print sections. Adjusting the retraction distance and speed can further help minimize stringing. Using a lower printing temperature can also reduce oozing, as high temperatures cause filament to flow too easily.
Another effective method is to increase travel speed, so the nozzle moves faster between sections, reducing the chances of filament oozing. If stringing persists, using a different filament brand with better flow properties or applying a post-processing heat gun technique can remove unwanted strings and refine the print’s final appearance.
Resolving Warping and Print Detachment Issues
Warping is a common problem where the edges of a print lift off the bed, leading to distorted or failed prints. This typically happens due to rapid cooling, causing uneven contraction of the filament. A simple fix is to use a heated bed and set it to the recommended temperature for the filament type being used. Adding an adhesive such as glue stick, painter’s tape, or a PEI sheet can also improve bed adhesion and prevent warping.
Additionally, using an enclosure to maintain a stable temperature around the print can prevent warping, especially when printing with materials like ABS. Lowering the cooling fan speed during the first few layers can also help the print adhere better to the bed. By implementing these quick fixes, print detachment and warping issues can be significantly reduced.
Smoothing Rough or Inconsistent Print Surfaces
A rough or inconsistent print surface can be caused by improper layer height settings, vibrations, or inconsistent filament flow. A quick fix is to lower the layer height to produce finer details and smoother surfaces. Ensuring the printer is placed on a stable surface can minimize vibrations that cause print imperfections. Regularly checking for loose belts and tightening them can also improve print quality.
Another method to smooth prints is post-processing techniques such as sanding, acetone vapor smoothing (for ABS prints), or using a heat gun. If prints exhibit inconsistencies, checking filament quality and ensuring the spool is not tangled can prevent uneven extrusion. By fine-tuning slicer settings and maintaining printer components, achieving high-quality, smooth prints becomes much easier.
What's Your Reaction?
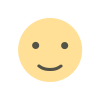
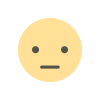
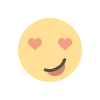
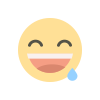
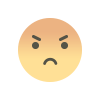
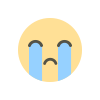
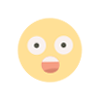