Jute Bag Manufacturing Plant Project Report 2025: Manufacturing Plant Setup and Operations

Introduction
Jute bags, made from the natural fiber derived from the jute plant, have gained significant popularity due to their eco-friendly and sustainable properties. As the world becomes increasingly aware of the harmful effects of plastic pollution, the demand for biodegradable and recyclable alternatives like jute bags has soared. The Jute Bag Manufacturing Plant Project Report aims to provide insights into setting up a plant for the production of jute bags, covering essential aspects such as raw materials, production processes, market trends, and financial considerations.
Market Overview
The global market for jute bags is growing rapidly as more consumers and businesses turn toward sustainable alternatives to plastic. The increasing awareness of environmental concerns, along with government regulations restricting plastic use, has contributed to the surge in demand for jute bags. The versatility of jute bags, ranging from shopping bags to promotional bags, makes them highly marketable across various sectors, including retail, agriculture, and corporate gifting.
-
Environmental Concerns: The growing awareness about plastic pollution has led to an increased preference for eco-friendly products, such as jute bags. Jute is a natural fiber that is biodegradable, compostable, and recyclable, making it an ideal alternative to plastic bags.
-
Government Regulations: Many countries and regions are implementing stricter regulations on plastic use, which has accelerated the shift toward jute bags. For example, several countries have banned single-use plastic bags, further promoting the demand for jute alternatives.
-
Retail and Fashion: Retailers, including grocery stores, boutiques, and online stores, are increasingly offering jute bags to customers as an eco-friendly packaging solution. The fashion industry also embraces jute bags as part of sustainable fashion trends, further expanding the market.
-
Promotional and Corporate Gifting: Jute bags are widely used in the promotional sector, with businesses opting for customized jute bags to promote their brands. Custom printing and branding make jute bags a popular choice for corporate gifting.
-
Durability and Cost-Effectiveness: Jute bags are durable, reusable, and cost-effective, which makes them an attractive option for both consumers and manufacturers. Unlike single-use plastic bags, jute bags can be used for multiple purposes and have a longer lifespan.
Get a Free Sample Report with Table of Contents@
Raw Materials
The primary raw material for jute bag manufacturing is jute fiber, a natural and biodegradable material extracted from the jute plant. In addition to jute, several other raw materials are used in the manufacturing process to produce finished jute bags. These include:
-
Jute Fiber: The main material used to make jute bags. Jute is cultivated primarily in countries like India, Bangladesh, and China. It is harvested and processed into yarns that are woven into fabric.
-
Dyeing and Printing Materials: These are used for adding color and designs to the jute fabric. The dyeing process involves using eco-friendly dyes to ensure the bags remain environmentally sustainable.
-
Thread and Sewing Materials: To stitch the jute fabric and create the bag structure, high-quality threads and other sewing materials are required. Cotton threads are often used, as they are natural and complement the eco-friendly nature of jute.
-
Hardware and Accessories: Zippers, buttons, handles, and straps are often added to enhance the functionality of the jute bags. These materials can be made from various materials such as metal, plastic, or wood, depending on the design requirements.
-
Packaging Materials: For packaging the final product, plastic or cardboard packaging may be required, though it is advisable to minimize plastic use by opting for recyclable or biodegradable alternatives.
Manufacturing Process
The production of jute bags involves several stages, from the preparation of raw materials to the final stitching and packaging of the product. Below are the typical steps involved in the manufacturing process:
Step 1: Harvesting and Preparing Jute Fiber
Jute is primarily grown in tropical regions and harvested during the monsoon season. The harvested jute plants are stripped of their bark, and the fiber is extracted. This fiber is then processed into jute yarns through a series of cleaning, retting, and drying processes. The yarns are then ready for weaving or knitting into jute fabric.
Step 2: Weaving or Knitting Jute Fabric
The jute yarns are woven into fabric using looms or machines, depending on the scale of production. The fabric produced can vary in thickness, density, and texture, depending on the intended use of the final product. Some manufacturers may also opt to knit the yarns into fabric.
Step 3: Dyeing and Printing
Once the jute fabric is woven, it may be dyed to achieve the desired color. Eco-friendly dyes are used to ensure that the bags remain safe for the environment. After dyeing, the fabric may undergo a printing process where logos, branding, or decorative patterns are added using screen printing or digital printing techniques.
Step 4: Cutting the Fabric
The dyed and printed fabric is then cut into the required size and shape. Different designs, such as tote bags, shopping bags, or promotional bags, may have different patterns, and the fabric is cut accordingly. Cutting is usually done using manual or automatic cutting machines.
Step 5: Stitching and Assembly
The cut pieces of fabric are sewn together to form the bag. Sewing machines are used to stitch the sides, handles, and other parts of the bag. Reinforced stitching may be used at the seams and handles to ensure durability and strength, especially for larger bags.
Step 6: Adding Accessories
In this step, accessories like zippers, buttons, buckles, or handles are added to the jute bag, depending on the design. This may involve additional stitching, gluing, or other attachment methods.
Step 7: Finishing and Quality Control
After the bags are assembled, they undergo finishing processes such as ironing, smoothing, and trimming. Quality control checks are carried out to ensure that the bags meet the required standards of durability, appearance, and functionality. Any defective bags are removed from the production line.
Step 8: Packaging and Shipping
Once the jute bags are finished, they are packaged for distribution. Packaging is usually done in bulk, and the bags are often packed in cardboard boxes or other recyclable materials. The bags are then ready to be shipped to retailers, wholesalers, or customers.
Equipment Requirements
Setting up a jute bag manufacturing plant requires a range of equipment and machinery to carry out the various stages of production. These include:
-
Jute Spinning Machines: These machines are used to spin raw jute fibers into yarns that can be woven into fabric.
-
Weaving Looms: Used for weaving the jute yarns into fabric. These can be manual or automatic, depending on production capacity.
-
Dyeing Machines: Machines for dyeing the jute fabric to achieve the desired color. These machines ensure an even distribution of color across the fabric.
-
Printing Machines: Used for printing designs, logos, or patterns on the jute fabric using eco-friendly dyes.
-
Cutting Machines: Automatic or manual cutting machines to cut the jute fabric into specific sizes and shapes for bags.
-
Sewing Machines: Heavy-duty industrial sewing machines to stitch the cut fabric pieces into bags.
-
Finishing Equipment: Ironing and smoothing machines to ensure the final product is wrinkle-free and of high quality.
-
Packaging Machines: Used for packaging the finished jute bags into cartons for shipment.
Regulatory Considerations
The jute bag manufacturing industry is subject to various regulations and standards, especially related to product quality, safety, and environmental sustainability. Some of the key regulations include:
-
Environmental Regulations: Manufacturers must comply with local and international environmental regulations, ensuring that their production processes do not cause harm to the environment. This includes the responsible disposal of waste, water management, and minimizing plastic usage.
-
Quality Standards: Jute bags intended for consumer use must meet quality standards in terms of durability, material composition, and functionality. Certification from authorities such as ISO or local regulatory bodies may be required.
-
Labor Laws: Manufacturers must comply with labor laws related to wages, working conditions, and safety standards for employees working in the production plant.
-
Labeling Regulations: Proper labeling of the jute bags is essential to provide customers with accurate information about the product, including material composition, care instructions, and brand information.
Financial Considerations
Setting up a jute bag manufacturing plant requires significant investment in infrastructure, machinery, raw materials, and labor. The key financial aspects include:
-
Capital Investment: The initial investment in land, factory construction, machinery, and raw materials is substantial. The scale of the plant and production capacity will influence this cost.
-
Operational Costs: Ongoing costs include raw material procurement, labor, utilities, packaging, maintenance, and transportation. Efficient management of these costs is crucial to achieving profitability.
-
Revenue and Profitability: The revenue generated from the sale of jute bags will depend on factors such as production volume, pricing strategy, and market demand. Profitability can be enhanced by targeting both domestic and international markets, as well as offering customized bags for promotional purposes.
-
Return on Investment (ROI): The ROI for a jute bag manufacturing plant is generally high, especially with the growing demand for eco-friendly products. However, profitability depends on the ability to scale production, optimize costs, and maintain high product quality.
Media Contact
Company Name: Claight Corporation
Contact Person: Lewis Fernandas, Corporate Sales Specialist — U.S.A.
Email: sales@expertmarketresearch.com
Toll Free Number: +1–415–325–5166 | +44–702–402–5790
Address: 30 North Gould Street, Sheridan, WY 82801, USA
Website: www.expertmarketresearch.com
Aus Site: https://www.expertmarketresearch.com.au
What's Your Reaction?
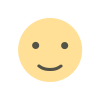
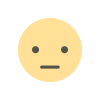
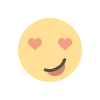
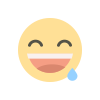
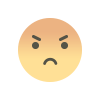
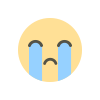
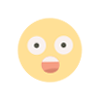